How To Reduce Downtime Through Maintenance
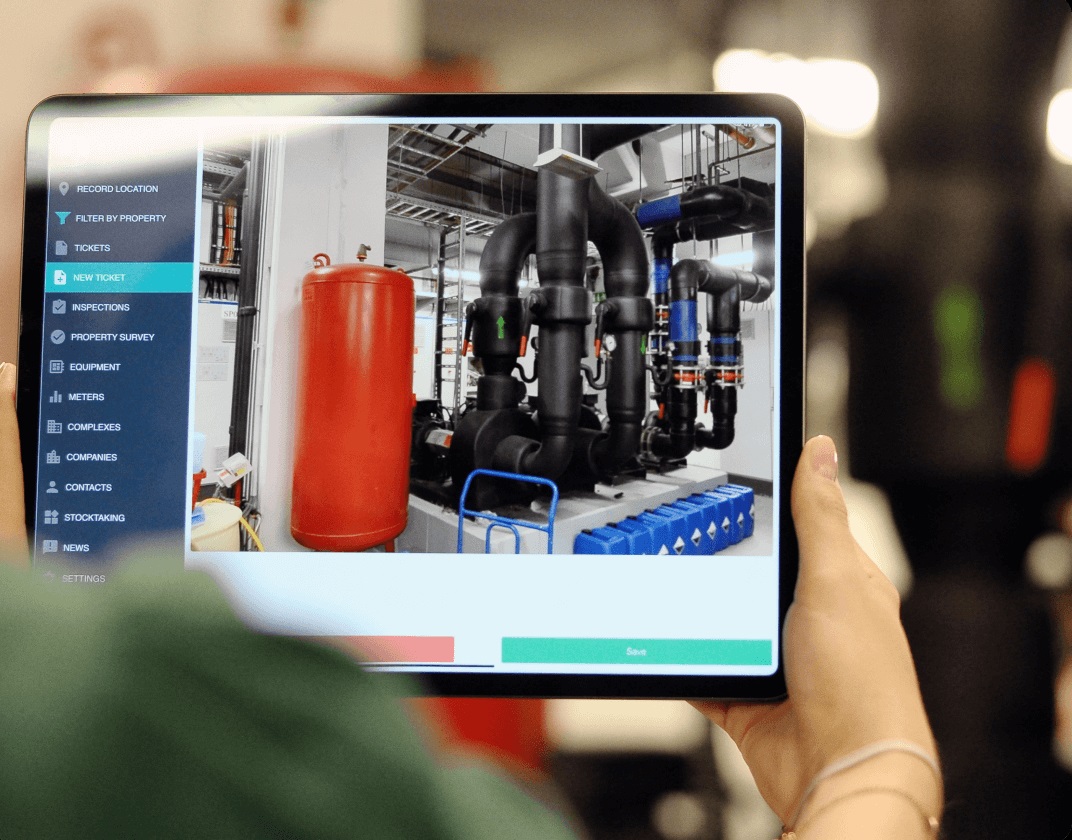
Equipment maintenance could be quite costly in terms of time and money. How can competitiveness be upheld while generating a return on investment (ROI)? Here, we take a quick look at the managerial tactics and technological developments used to reduce equipment and maintenance downtime.
The market for maintenance, repair, and operations is predicted to reach a value of $701.3 billion by 2026. The factors that contribute to this high expense in industrial settings are numerous. Aging assets are mostly to blame for unplanned downtime. According to maintenance experts, unscheduled equipment downtime can be caused by mechanical failure, operator mistake, a lack of adequate maintenance time, and bad design.
Installing components with low or no maintenance requirements is one way to reduce the need for maintenance. Ultrasonic clamp-on meters are one illustration of this. These meters are used in a variety of settings, including the water distribution industry, because they don’t have any moving elements that can deteriorate with time. They are designed to need little or no upkeep.
A thorough preventive maintenance (PM) strategy could be another way to boost ROI. In fact, 76 percent of industrial enterprises prioritized preventive maintenance in 2020. This schedule-based approach aims to identify prospective problems before they have a chance to become problems. Thus, PM helps to decrease downtime, increase equipment life, and boost resale value. Nevertheless, depending on the kind of machinery, it increases the asset’s total cost of ownership.
Predictive maintenance also uses analytical technologies. Studies show that 41{d76f1c19516befd0d02dd7628c4f02994b77c2f36ca1cda12e5887cc42cc72f7} of industrial enterprises presently employ this strategy. Predictive maintenance is reportedly very cost-effective, despite being expensive and new. When compared to preventive maintenance, it can save between 8 and 11{d76f1c19516befd0d02dd7628c4f02994b77c2f36ca1cda12e5887cc42cc72f7}, according to the US Department of Energy. Additionally, it is anticipated that the global market for predictive maintenance will reach $23.5 billion by 2024.
Predictive maintenance (PdM) is what. PdM uses specialized software, artificial intelligence, and sensors to assess the health of in-service assets and provide data in real-time. It is possible to forecast when the asset needs maintenance by looking at this data. By performing tasks only when necessary, this strategy seeks to potentially reduce expenses in comparison to routine or time-based preventative maintenance.
Managing maintenance is a difficult task. However, it is feasible to increase the lifespan and performance of commonplace equipment by using the right tools for the job, using new technologies, and upgrading to components with low- to no-maintenance.
Please refer to the additional material for more details on maintenance and viable solutions.